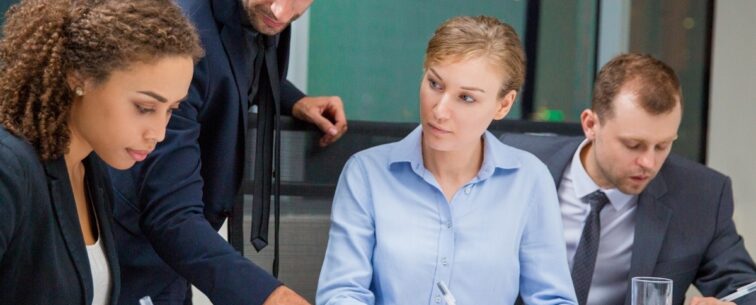
Case Study: Digitization of the Welding Inspection Process in the Automobile Industry
Project Timeline: March 2022 – June 2022
Client: Automobile Manufacturer
Technology Stack: Oracle Production Database, SQL Server 2016 (Data Warehouse), Power BI (Dashboard)
Overview
An automobile manufacturer sought to enhance its welding inspection process by migrating from Welding Andon-SAP Business Objects (BO) to Power BI. The goal of this project was to digitize inspection activities, improve quality control, and increase inspector efficiency through real-time reporting and data analysis.
Challenge
The client faced several challenges in their existing welding inspection process:
- Inefficient Manual Processes: The reliance on paperwork and manual inspection records resulted in time-consuming processes and increased chances of errors.
- Lack of Focus on Critical Areas: Inspectors had difficulty identifying specific welds that required immediate attention, which hindered quality control efforts.
- Delayed Decision-Making: The absence of real-time data made it challenging to make timely decisions based on inspection results.
To address these issues, the client required a modernized solution that would streamline the inspection process and enhance overall quality and efficiency.
Solution
SQL Orbit executed a migration project that transitioned the welding inspection process from Welding Andon-SAP BO to Power BI. Key elements of the solution included:
- Real-Time Data Integration: By leveraging Oracle Production Database and SQL Server 2016, a centralized data warehouse was established, enabling real-time access to inspection data and metrics.
- Interactive Power BI Dashboards: Custom dashboards were developed in Power BI to visualize inspection activities, allowing inspectors to monitor performance and focus on welds that needed immediate attention.
- Automated Reporting: The new solution eliminated paperwork and streamlined reporting processes, reducing time spent on administrative tasks and enabling inspectors to concentrate on quality assurance.
Outcomes
The implementation of the Power BI solution led to significant improvements in the welding inspection process, with measurable benefits including:
- Reduction in Inspection Time and Effort
- The time and effort required for inspection activities were reduced by 30%, allowing inspectors to focus on critical areas and improving workflow efficiency.
- Enhanced Quality Control
- Quality improvements of 35% were achieved by directing attention to welds that required inspection, which led to a 20% reduction in errors during the welding process.
- Improved Decision-Making
- Access to up-to-date information in real-time resulted in a 15% improvement in decision-making capabilities for inspectors and management.
- Increased Inspector Efficiency
- Inspector efficiency improved by 20%, as the enhanced quality and streamlined processes allowed for more inspections to be completed in less time.
Benefits
- Streamlined Processes: The migration to Power BI significantly digitized the inspection process, eliminating paperwork and automating reporting, which improved overall operational efficiency.
- Real-Time Insights: Inspectors were equipped with real-time data to make informed decisions, focusing their efforts on areas needing improvement.
- Higher Quality Standards: The project led to a stronger focus on quality control, enhancing the overall production standards within the automobile manufacturing process.